In che modo la tua azienda determina i punti, le tolleranze e la frequenza dei test di calibrazione? Una semplice regola empirica è quella di calibrare gli strumenti al 10, 50 e 90% del fondo scala e di utilizzare una tolleranza pari a 1,5 o 2 volte quella del produttore. Molte aziende standardizzano le frequenze per calibrare tutti gli strumenti critici ogni sei mesi e quelli non critici una volta all’anno. Sebbene questo approccio possa facilitare l’inserimento di nuovi strumenti nel programma di taratura e la gestione del calendario di taratura, potrebbe creare lavoro extra e costare tempo e denaro.
In questo articolo parleremo dell’utilizzo di un approccio basato sul rischio per determinare l’intervallo di calibrazione, la tolleranza, la frequenza e la criticità utilizzando la Guida alle Buone Pratiche di Fabbricazione Automatizzata (GAMP) dell’International Society of Pharmaceutical Engineers (ISPE), insieme a suggerimenti e strumenti che possono essere utilizzati per l’implementazione. Seguendo la guida GAMP dell’ISPE, il tuo programma di calibrazione sarà conforme all’iniziativa promossa dalla Food & Drug Administration (FDA) di un approccio basato sul rischio alle buone pratiche di fabbricazione (GMP) nel 21° secolo. Questo approccio si concentra sui rischi per la qualità del prodotto e per la sicurezza pubblica e spesso può consentire alla tua organizzazione di risparmiare sui costi.
La spina dorsale di questo programma dipende dal prendere le decisioni corrette sulla base di informazioni affidabili, accurate e tracciabili. Le informazioni necessarie si trovano nelle specifiche dei requisiti dell’utente (URS), nei protocolli di convalida e in altri documenti creati e approvati al momento dello sviluppo del processo produttivo. Questi documenti vengono utilizzati per soddisfare i requisiti della FDA in base alle seguenti decisioni:
- Se il farmaco è sicuro ed efficace per l’uso proposto e se i benefici del farmaco superano i rischi.
- Se l’etichettatura proposta per il farmaco è appropriata e cosa dovrebbe contenere
- Se i metodi di produzione del farmaco e i controlli utilizzati per mantenerne la qualità sono adeguati a preservarne l’identità, la forza, la qualità e la purezza.
Completoing valutazioni del rischio di i tuoi strumenti utilizzando il programma sopra citato documenti volontà determinare il corretto criticità, frequenza di calibrazione, punti di prova e tolleranzas basati su dati scientifici, non una regola empirica o una congettura. It also helps garantire le risorse siano concentrate nelle aree più critiche della struttura per massimizzare l’utilizzo e ridurree costi.
Il primo passo consiste nel riunire un team per eseguire le valutazioni dei rischi, che dovrebbe comprendere:
- Ingegnere di processo/sistema – identifica i parametri e i limiti, le fasi critiche del processo e le tolleranze del processo. Saranno inoltre responsabili dell’approvazione delle specifiche e delle frequenze di calibrazione e dell’approvazione delle valutazioni dei rischi.
- Specialisti in calibrazione/metrologia – avviano e gestiscono il processo di valutazione del rischio, sviluppano le specifiche e le frequenze di calibrazione, selezionano e approvano gli strumenti appropriati per soddisfare i requisiti del processo, impostano la strategia di calibrazione e approvano le valutazioni del rischio.
- Assicurazione della qualità: garantisce che i parametri e i limiti del processo siano conformi alla normativa, esamina le specifiche e le frequenze di calibrazione per verificare la conformità con le procedure del sito e l’approvazione finale delle valutazioni del rischio.
Dopo aver riunito la squadra, scarica un rapporto dal tuo Computer Manutenzione Msistema di gestione (CMMS) che include gli strumenti per il processo o il sistema valuterai. Sarà utile che il rapporto includa informazioni che si riferiscono a la posizione di misurazione nel processo/sistema, il produttore e numero di modello del installato strumento, e il specifiche di calibrazione attuali. La valutazione del rischio processos Risponderà a diverse domande a determinare il calibrazione corretta processo, limiti, e la frequenza. Di seguito è riportato una panoramica del processo di valutazione del rischio.
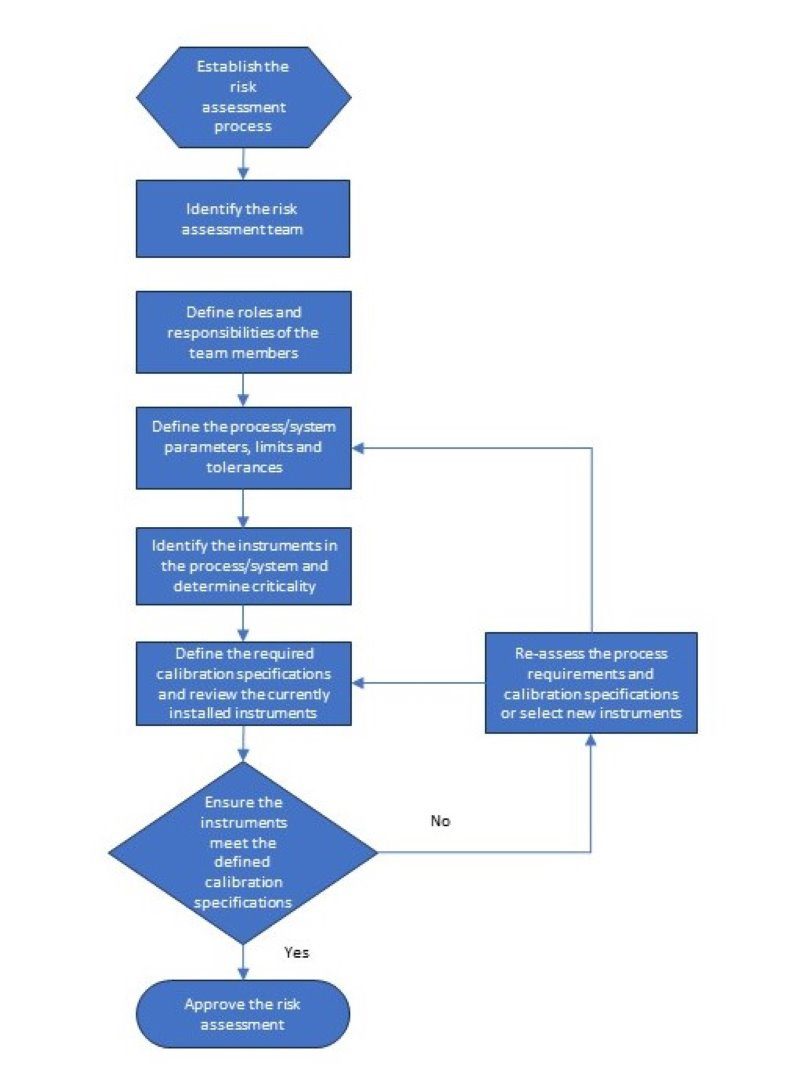
È necessario redigere una SOP che specifichi come deve essere completata la valutazione dei rischi e quali informazioni sono necessarie. Di seguito sono elencate le informazioni necessarie per completare una valutazione dei rischi e un esempio di processo di valutazione.
- ID strumento
- Descrizione dello strumento
- Produttore dello strumento, modello e numero di serie
- Gamma e precisione dello strumento
- In quale sistema/processo è installato lo strumento
- Campo di processo, campo operativo e tolleranza
- Criticità dello strumento
- Intervallo di calibrazione, punti di test e tolleranza
- Frequenza di calibrazione
- Firme dei membri del team di valutazione dei rischi
La maggior parte delle informazioni di cui sopra proviene dagli strumenti installati e dalla documentazione di processo. Le specifiche di calibrazione vengono determinate rispondendo a domande come quelle che seguono.
- Criticità dello strumento (può essere stata precedentemente determinata da una valutazione d’impatto):
- Lo strumento viene utilizzato per la pulizia e/o la sterilizzazione delle apparecchiature?
- Un fallimento avrebbe un impatto sulla qualità del prodotto o sulla sicurezza del paziente?
- Un fallimento avrebbe un impatto sull’efficacia del processo o su altri aspetti aziendali?
- Un guasto potrebbe creare un impatto sulla sicurezza o sull’ambiente?
Se la risposta a una qualsiasi delle domande precedenti è “sì”, lo strumento viene classificato come critico. Se la risposta a tutte le domande è “no”, lo strumento viene classificato come non critico.
- Intervallo di calibrazione: dovrebbe essere leggermente più ampio dell’intervallo di processo, o dell’intervallo di allarme se applicabile, per garantire l’accuratezza all’interno dell’intervallo operativo. Se l’intervallo operativo non è stato definito o non è noto, si consiglia di calibrare l’intero intervallo dello strumento.
- I punti di prova della calibrazione devono trovarsi agli estremi basso e alto dell’intervallo di calibrazione e contenere almeno un punto all’interno dell’intervallo operativo.
- La tolleranza di calibrazione deve essere superiore all’accuratezza del produttore e inferiore alla tolleranza del processo.
- La frequenza di calibrazione può basarsi su fattori di rischio come questi:
-
- Se si verifica un guasto, qual è l’impatto sul rilascio del prodotto?
- Se si verifica un guasto, quanta rilavorazione del prodotto è disposta ad accettare la tua azienda?
- Se si verifica un fallimento, qual è l’impatto ambientale che la tua azienda è disposta ad accettare?
- Disponi di dati storici in loco per lo stesso produttore e modello di strumento?
Grazie a un esercizio come questo, i tuoi strumenti avranno una maggiore accuratezza e precisione in tutto l’intervallo operativo e completare le indagini fuori tolleranza diventerà più facile ora che hai una motivazione documentata di come lo strumento influisce sul processo. Inoltre, la maggior parte delle aziende stabilisce che alcuni, se non la maggior parte, dei propri strumenti critici non hanno bisogno di essere calibrati ogni 6 mesi. Alcune aziende scelgono anche di estendere la frequenza di calibrazione degli strumenti non critici a 18-24 mesi. Un altro metodo utilizzato per estendere la frequenza di calibrazione è l’utilizzo di dati storici. In questo caso si stabilisce una frequenza di calibrazione iniziale e, dopo aver completato la terza calibrazione, si esegue una revisione dei dati. Se lo strumento supera tutte e tre le calibrazioni senza alcuna regolazione, la frequenza può essere estesa del 50 o del 100%. Di seguito è riportato un esempio di estensione della frequenza di calibrazione.
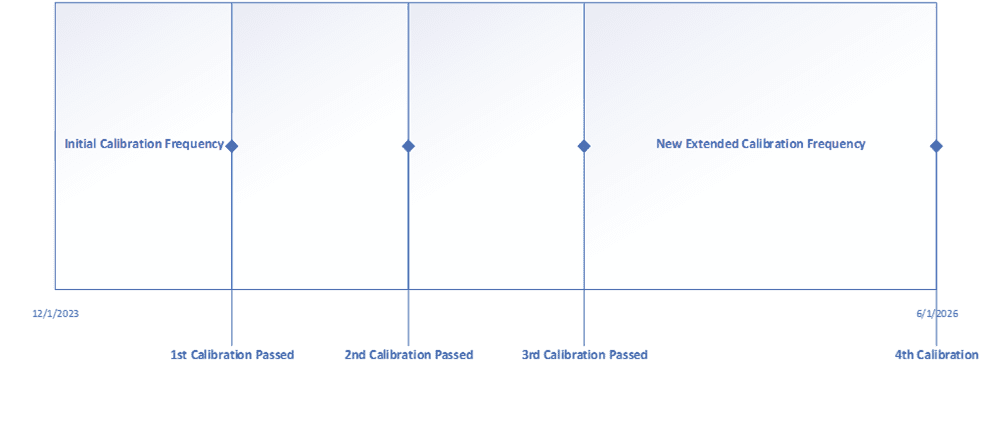
L’estensione delle frequenze di calibrazione è il punto in cui i risparmi saranno più evidenti, in quanto un minor numero di eventi di calibrazione durante l’anno significa che le risorse possono svolgere altre attività. La cosa importante da ricordare è di aggiornare tutte le procedure esistenti che impongono le frequenze di calibrazione.
Se la tua azienda vuole trarre beneficio dall’implementazione di un approccio alla calibrazione basato sul rischio, CAI è pronta ad aiutarti. CAI vanta un’esperienza interfunzionale in materia di convalida, qualità, prestazioni umane, gestione dei progetti, manutenzione e calibrazione. Diventiamo il tuo partner di fiducia nella gestione delle risorse GMP.