Wie legt Ihr Unternehmen die Testpunkte, Toleranzen und Häufigkeit der Kalibrierung fest? Eine einfache Faustregel besagt, dass Instrumente bei 10, 50 und 90 % des vollen Messbereichs kalibriert werden und eine Toleranz von 1,5 oder 2 mal der Herstellertoleranz verwendet wird. Viele Unternehmen standardisieren die Häufigkeit der Kalibrierungen, so dass alle kritischen Instrumente alle sechs Monate und nicht kritische Instrumente einmal pro Jahr kalibriert werden. Dieser Ansatz mag zwar die Aufnahme neuer Instrumente in das Kalibrierungsprogramm und die Verwaltung des Kalibrierungszeitplans vereinfachen, er könnte jedoch zusätzliche Arbeit verursachen und Sie Zeit und Geld kosten.
In diesem Artikel erörtern wir die Verwendung eines risikobasierten Ansatzes zur Bestimmung von Kalibrierungsbereich, Toleranz, Häufigkeit und Kritikalität unter Verwendung des Leitfadens der International Society of Pharmaceutical Engineers (ISPE) für die Gute Automatisierte Herstellungspraxis (GAMP) sowie Tipps und Tools, die für die Umsetzung verwendet werden können. Die Befolgung des ISPE GAMP-Leitfadens stellt sicher, dass Ihr Kalibrierungsprogramm die von der Food & Drug Administration (FDA) geförderte Initiative eines risikobasierten Ansatzes für die Gute Herstellungspraxis (GMP) im 21. Jahrhundert. Dieser Ansatz konzentriert sich auf die Risiken für die Produktqualität und die öffentliche Sicherheit und kann Ihrem Unternehmen oft Kosteneinsparungen bringen.
Das Rückgrat eines solchen Programms hängt davon ab, dass die richtigen Entscheidungen auf der Grundlage zuverlässiger, genauer und nachvollziehbarer Informationen getroffen werden. Die erforderlichen Informationen finden Sie in User Requirement Specifications (URS), Validierungsprotokollen und anderen Dokumenten, die erstellt und genehmigt wurden, als der Herstellungsprozess entwickelt wurde. Diese Dokumente werden verwendet, um die Anforderungen der FDA auf der Grundlage der folgenden Entscheidungen zu erfüllen:
- Ob das Medikament in der/den vorgeschlagenen Anwendung(en) sicher und wirksam ist und ob der Nutzen des Medikaments die Risiken überwiegt.
- ob die vorgeschlagene Kennzeichnung des Medikaments angemessen ist und was sie enthalten sollte
- ob die bei der Herstellung des Medikaments angewandten Methoden und die zur Aufrechterhaltung der Qualität des Medikaments durchgeführten Kontrollen ausreichend sind, um die Identität, Stärke, Qualität und Reinheit des Medikaments zu erhalten
Completing Risikobewertungen von Ihre Instrumente unter Verwendung der Die oben erwähnte Dokumente wird bestimmen die richtige Kritikalität, Kalibrierungsfrequenz, Testpunkte, und Toleranzs basierend auf wissenschaftlichen Daten, keine Faustformel oder Vermutung. It also helps sicherstellen Ressourcen sind konzentriert in den kritischsten Bereichen Ihrer Einrichtung zur Maximierung der Auslastung und zu reduzierene Kosten.
Der erste Schritt besteht darin, ein Team zusammenzustellen, das die Risikobewertungen durchführt, zu dem auch Sie gehören sollten:
- Prozess-/Systemtechniker – identifizieren Parameter und Grenzwerte, kritische Prozessschritte und Prozesstoleranzen. Sie sind auch für die Genehmigung der Kalibrierungsspezifikationen und -häufigkeiten sowie für die Genehmigung der Risikobewertungen verantwortlich.
- Kalibrierungs-/Metrologiespezialisten – initiieren und verwalten den Prozess der Risikobewertung, entwickeln die Kalibrierungsspezifikationen und -häufigkeiten, wählen und genehmigen die geeigneten Instrumente, um die Prozessanforderungen zu erfüllen, legen die Kalibrierungsstrategie fest und genehmigen die Risikobewertungen.
- Qualitätssicherung – Sicherstellung, dass die Prozessparameter und -grenzwerte den behördlichen Vorgaben entsprechen, Überprüfung der Kalibrierungsspezifikationen und -häufigkeiten auf Übereinstimmung mit den Verfahren vor Ort und die endgültige Genehmigung der Risikobewertungen.
Nachdem Sie das Team zusammengestellt haben, Herunterladen einer Bericht von Ihrem Computer Wartung Management-System (CMMS) dass enthält die Instrumente für den Prozess oder das System werden Sie bewerten. Es wäre hilfreich, wenn der Bericht Folgendes enthält Informationen in Bezug auf den Ort der Messung im Prozess/System, die Hersteller und Modellnummer des installiert Instrument, und die aktuelle Kalibrierungsspezifikationen. Die Risikobewertung prozessierens wird die Beantwortung mehrerer Fragen beinhalten zu bestimmen die korrekte Kalibrierung Prozess, Grenzen, und Frequenz. Unten ist einen Überblick über den Prozess der Risikobewertung.
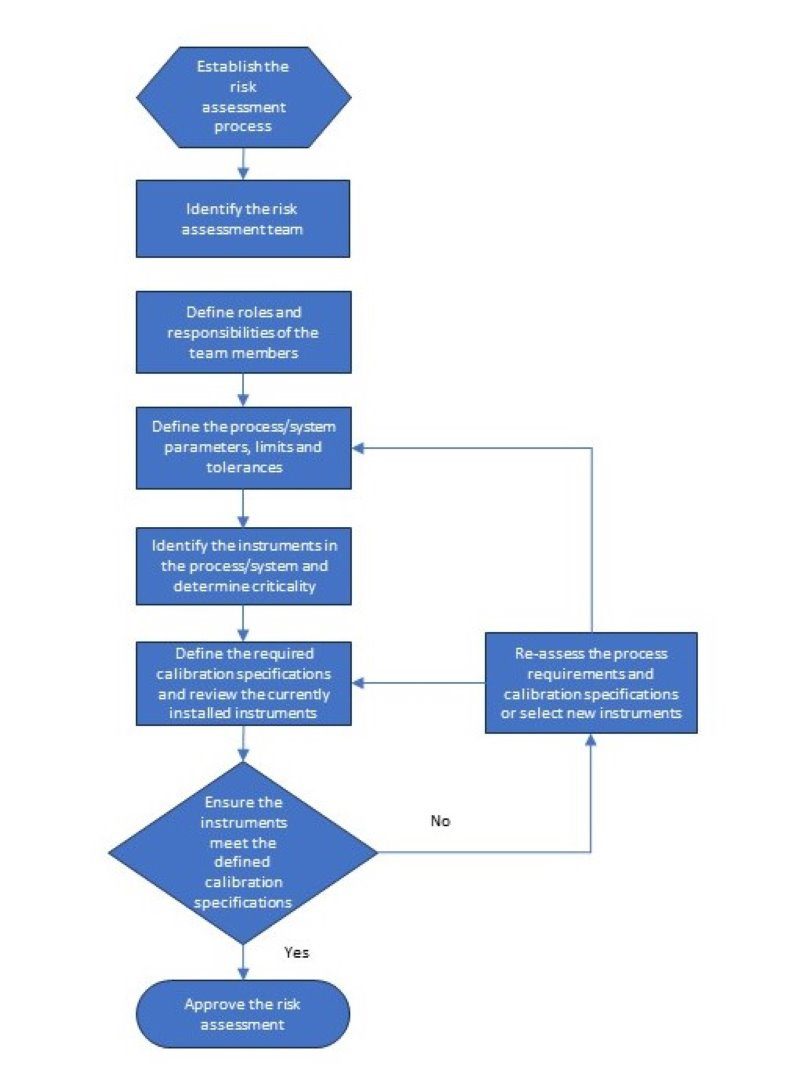
Es sollte eine Arbeitsanweisung erstellt werden, in der detailliert beschrieben wird, wie die Risikobewertung durchgeführt werden sollte und welche Informationen erforderlich sind. Nachfolgend finden Sie eine Liste der Informationen, die für eine Risikobewertung erforderlich sind, sowie ein Beispiel für einen Bewertungsprozess.
- Instrument ID
- Beschreibung des Instruments
- Hersteller, Modell und Seriennummer des Geräts
- Reichweite und Genauigkeit des Geräts
- In welchem System/Prozess ist das Instrument installiert?
- Prozessbereich, Betriebsbereich & Toleranz
- Kritikalität des Instruments
- Kalibrierungsbereich, Testpunkte & Toleranz
- Frequenz der Kalibrierung
- Unterschriften der Mitglieder des Risikobewertungsteams
Die meisten der oben genannten Informationen stammen aus den installierten Geräten und der Prozessdokumentation. Die Kalibrierungsspezifikationen werden durch die Beantwortung von Fragen wie den folgenden bestimmt.
- Kritikalität des Instruments (kann zuvor durch eine Folgenabschätzung ermittelt worden sein):
- Wird das Instrument zur Reinigung und/oder Sterilisation von Geräten verwendet?
- Würde ein Fehler die Produktqualität oder die Patientensicherheit beeinträchtigen?
- Würde sich ein Ausfall auf die Effektivität des Prozesses oder andere geschäftliche Aspekte auswirken?
- Würde ein Ausfall die Sicherheit oder die Umwelt beeinträchtigen?
Wenn die Antwort auf eine der oben genannten Fragen „ja“ lautet, wird das Instrument als kritisch eingestuft. Lautet die Antwort auf alle Fragen „nein“, dann wird das Instrument als unkritisch eingestuft.
- Kalibrierungsbereich: sollte etwas größer sein als der Prozessbereich oder ggf. der Alarmbereich, um die Genauigkeit innerhalb des Betriebsbereichs zu gewährleisten. Wenn der Betriebsbereich nicht definiert wurde oder unbekannt ist, wird empfohlen, den gesamten Bereich des Geräts zu kalibrieren.
- Die Kalibrierungstestpunkte sollten am unteren und oberen Ende des Kalibrierungsbereichs liegen und mindestens einen Punkt innerhalb des Betriebsbereichs enthalten.
- Die Kalibrierungstoleranz sollte größer als die Genauigkeit des Herstellers und kleiner als die Prozesstoleranz sein.
- Die Häufigkeit der Kalibrierung kann von Risikofaktoren wie diesen abhängen:
-
- Wenn ein Fehler auftritt, wie wirkt sich das auf die Produktfreigabe aus?
- Wenn ein Fehler auftritt, wie viel Nacharbeit ist Ihr Unternehmen bereit zu akzeptieren?
- Welche Auswirkungen auf die Umwelt ist Ihr Unternehmen bereit zu akzeptieren, wenn es zu einem Ausfall kommt?
- Haben Sie vor Ort historische Daten für denselben Hersteller und dasselbe Gerätemodell?
Durch eine Übung wie diese werden Ihre Instrumente über den gesamten Betriebsbereich hinweg eine höhere Genauigkeit und Präzision aufweisen, und der Abschluss von Untersuchungen bei Toleranzüberschreitungen wird einfacher, da Sie nun eine dokumentierte Begründung dafür haben, wie sich das Instrument auf den Prozess auswirkt. Außerdem stellen die meisten Unternehmen fest, dass einige, wenn nicht sogar die meisten ihrer kritischen Instrumente nicht alle 6 Monate kalibriert werden müssen. Einige Unternehmen entscheiden sich auch dafür, die Kalibrierungshäufigkeit von nicht kritischen Instrumenten auf 18 bis 24 Monate zu verlängern. Eine andere Methode zur Verlängerung der Kalibrierungshäufigkeit ist die Verwendung historischer Daten. In diesem Fall wird eine anfängliche Kalibrierungshäufigkeit festgelegt, und nach Abschluss der dritten Kalibrierung wird eine Überprüfung der Daten vorgenommen. Wenn das Gerät alle drei Kalibrierungen ohne Anpassung besteht, kann die Häufigkeit um 50 oder 100% verlängert werden. Nachfolgend finden Sie ein Beispiel für die Verlängerung der Kalibrierungshäufigkeit.
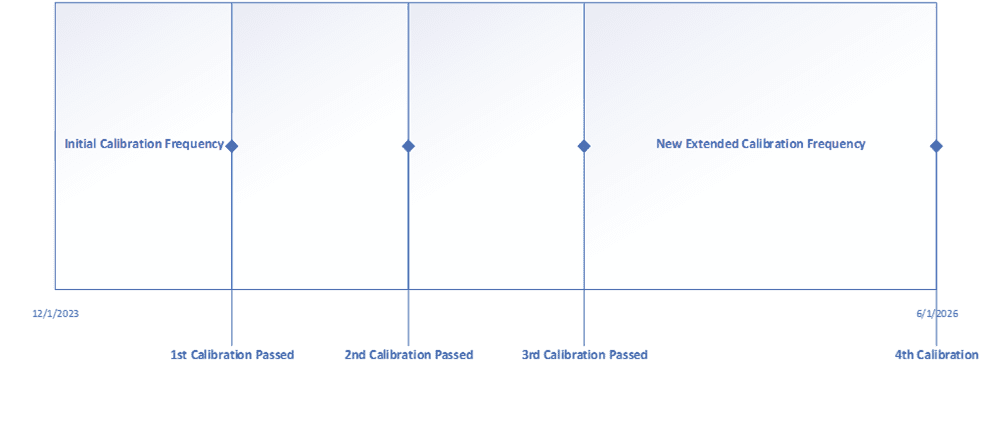
Die Ausweitung der Kalibrierungshäufigkeit ist der Punkt, an dem sich die Kosteneinsparungen am deutlichsten bemerkbar machen, da weniger Kalibrierungsereignisse im Laufe des Jahres bedeuten, dass die Ressourcen für andere Aktivitäten zur Verfügung stehen. Wichtig ist, dass Sie alle bestehenden Verfahren, die die Kalibrierungshäufigkeit vorschreiben, aktualisieren.
Wenn Ihr Unternehmen von der Einführung eines risikobasierten Ansatzes bei der Kalibrierung profitieren würde, würde CAI Ihnen gerne helfen. CAI verfügt über funktionsübergreifende Erfahrung in den Bereichen Validierung, Qualität, Human Performance, Projektmanagement sowie Wartung und Kalibrierung. Lassen Sie uns Ihr zuverlässiger Partner im GMP Asset Management werden.