¿Cómo determina tu organización los puntos de prueba de calibración, las tolerancias y la frecuencia? Una regla sencilla es calibrar los instrumentos al 10, 50 y 90% del rango a escala real y utilizar una tolerancia de 1,5 o 2 veces la tolerancia del fabricante. Muchas empresas estandarizan las frecuencias para calibrar todos los instrumentos críticos cada seis meses y los no críticos una vez al año. Aunque este planteamiento puede facilitar la incorporación de nuevos instrumentos al programa de calibración y la gestión del calendario de calibración, podría estar generando trabajo extra y costándote tiempo y dinero.
En este artículo hablaremos de la utilización de un enfoque basado en el riesgo para determinar el intervalo, la tolerancia, la frecuencia y la criticidad de la calibración utilizando la Guía de Buenas Prácticas de Fabricación Automatizada (GAMP) de la Sociedad Internacional de Ingenieros Farmacéuticos (ISPE), junto con consejos y herramientas que pueden utilizarse para su aplicación. Seguir la guía GAMP de la ISPE garantizará que tu programa de calibración cumpla la iniciativa promovida por la Administración de Alimentos y Medicamentos (FDA) de un enfoque basado en los riesgos para las Buenas Prácticas de Fabricación (BPF) en el siglo XXI. Este enfoque se centra en los riesgos para la calidad del producto y la seguridad pública, y a menudo puede suponer un ahorro de costes para tu organización.
La columna vertebral de un programa de este tipo depende de que se tomen las decisiones correctas basándose en información fiable, precisa y trazable. La información necesaria se encontrará en las Especificaciones de Requisitos de Usuario (URS), los protocolos de validación y otros documentos que se crearon y aprobaron cuando se desarrolló el proceso de fabricación. Estos documentos se utilizan para cumplir los requisitos de la FDA basándose en las siguientes decisiones:
- Si el medicamento es seguro y eficaz en el uso o usos propuestos, y si los beneficios del medicamento superan a los riesgos.
- Si el etiquetado propuesto para el medicamento es adecuado y qué debe contener
- Si los métodos utilizados en la fabricación del medicamento y los controles utilizados para mantener su calidad son adecuados para preservar la identidad, potencia, calidad y pureza del medicamento.
Completoing evaluaciones de riesgos de tus instrumentos utilizando el antes mencionada documentos se determina la adecuada criticidad, frecuencia de calibración, puntos de prueba, y tolerancias basada en datos científicos, no una regla empírica o conjetura. It also helps garantizar los recursos se concentrados en las áreas más críticas de tus instalaciones para maximizar utilización y reducire costes.
El primer paso es reunir un equipo para realizar las evaluaciones de riesgos, que debe incluir:
- Ingeniero de procesos/sistemas: identificará los parámetros y límites, los pasos críticos del proceso y las tolerancias del proceso. También se encargarán de aprobar las especificaciones y frecuencias de calibración y de aprobar las evaluaciones de riesgos.
- Especialistas en Calibración/Metrología: inician y gestionan el proceso de evaluación de riesgos, desarrollan las especificaciones y frecuencias de calibración, seleccionan y aprueban los instrumentos adecuados para cumplir los requisitos del proceso, establecen la estrategia de calibración y aprueban las evaluaciones de riesgos.
- Garantía de calidad: garantizar que los parámetros y límites del proceso cumplen la presentación reglamentaria, revisar las especificaciones y frecuencias de calibración para que cumplan los procedimientos del centro y la aprobación final de las evaluaciones de riesgos.
Después de reunir al equipo, descargar un informe de tu Ordenador Mantenimiento MSistema de gestión (GMAO) que incluye los instrumentos para el proceso o sistema evaluarás. Será útil que el informe incluya información relativo a el lugar de medición en el proceso/sistemala fabricante y número de modelo del instalado instrumento, y el especificaciones de calibración actuales. La evaluación de riesgos procesas incluirá responder a varias preguntas a determina el calibración correcta procesolímites, y frecuencia. A continuación una visión general del proceso de evaluación de riesgos.
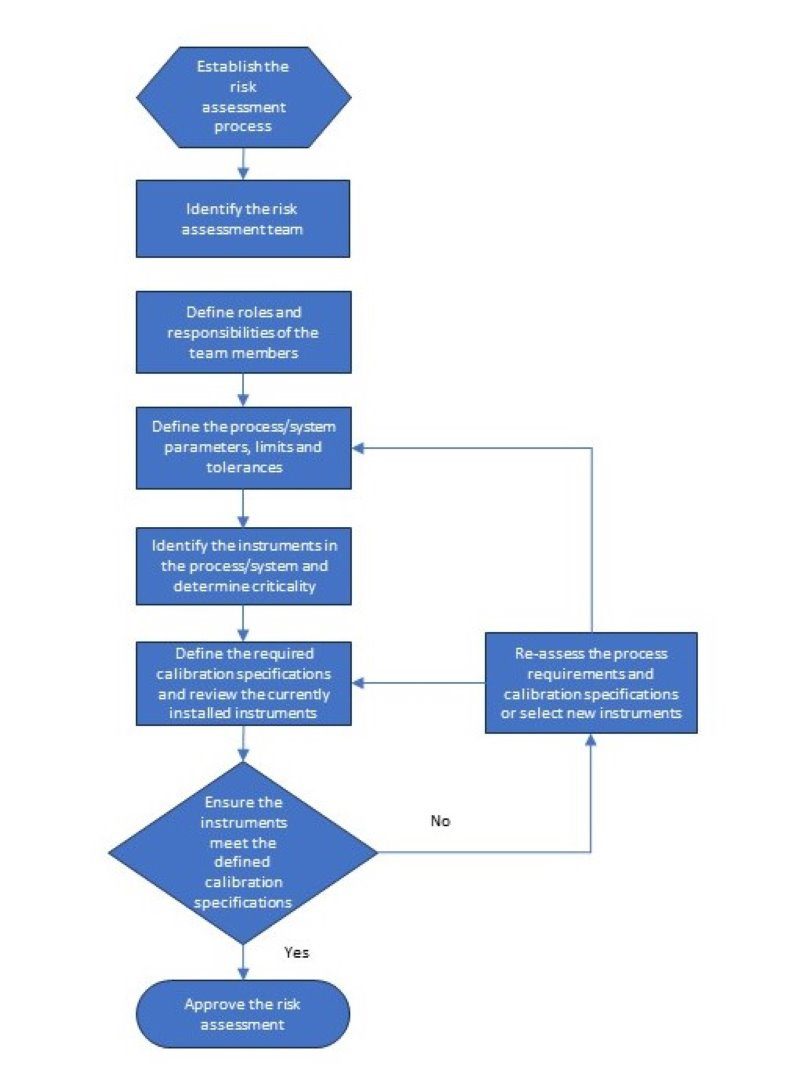
Debe redactarse un PNT que detalle cómo debe completarse la evaluación de riesgos y qué información se necesita. A continuación figura una lista de la información necesaria para completar una evaluación de riesgos, así como un ejemplo de proceso de evaluación.
- Identificación del instrumento
- Descripción del instrumento
- Fabricante del instrumento, modelo y número de serie
- Alcance y precisión del instrumento
- En qué sistema/proceso está instalado el instrumento
- Rango de proceso, rango de funcionamiento y tolerancia
- Criticidad del instrumento
- Rango de calibración, puntos de prueba y tolerancia
- Frecuencia de calibración
- Firmas de los miembros del equipo de evaluación de riesgos
La mayor parte de la información anterior procede de los instrumentos instalados y de la documentación del proceso. Las especificaciones de calibración se determinan respondiendo a preguntas como las siguientes.
- Criticidad del instrumento (puede haberse determinado previamente mediante una evaluación de impacto):
- ¿Se utiliza el instrumento para limpiar y/o esterilizar equipos?
- ¿Un fallo afectaría a la calidad del producto o a la seguridad del paciente?
- ¿Impactaría un fallo en la eficacia del proceso o en otro aspecto empresarial?
- ¿Crearía un fallo un impacto sobre la seguridad o el medio ambiente?
Si la respuesta a alguna de las preguntas anteriores es «sí», entonces el instrumento se clasifica como crítico. Si la respuesta a todas las preguntas es «no», entonces el instrumento se clasifica como no crítico.
- Intervalo de calibración: debe ser ligeramente más amplio que el intervalo del proceso, o el intervalo de alarma si procede, para garantizar la precisión dentro del intervalo de funcionamiento. Si no se ha definido un intervalo de funcionamiento o se desconoce, se recomienda calibrar todo el intervalo del instrumento.
- Los puntos de prueba de calibración deben estar en los extremos inferior y superior del intervalo de calibración y contener al menos un punto dentro del intervalo de funcionamiento.
- La tolerancia de calibración debe ser mayor que la precisión del fabricante y menor que la tolerancia del proceso.
- La frecuencia de calibración puede basarse en factores de riesgo como éstos:
-
- Si se produce un fallo, ¿cuál es el impacto en el lanzamiento del producto?
- Si se produce un fallo, ¿cuánta reelaboración del producto está dispuesta a aceptar tu empresa?
- Si se produce un fallo, ¿cuál es el impacto medioambiental que tu empresa está dispuesta a aceptar?
- ¿Tienes datos históricos in situ del mismo fabricante y modelo de instrumento?
Mediante un ejercicio como éste, tus instrumentos tendrán mayor exactitud y precisión en todo el rango de funcionamiento, y completar las investigaciones de fuera de tolerancia será más fácil ahora que tienes una justificación documentada de cómo afecta el instrumento al proceso. Además, la mayoría de las empresas determinan que algunos, si no la mayoría, de sus instrumentos críticos no necesitan calibrarse cada 6 meses. Algunas empresas también optan por ampliar la frecuencia de calibración de los instrumentos no críticos a entre 18 y 24 meses. Otro método utilizado para ampliar la frecuencia de calibración es el uso de datos históricos. En este caso, se establece una frecuencia de calibración inicial y, tras completar la tercera calibración, se realiza una revisión de los datos. Si el instrumento supera las tres calibraciones sin ajustes, la frecuencia puede ampliarse entonces en un 50 o un 100%. A continuación se muestra un ejemplo de ampliación de la frecuencia de calibración.
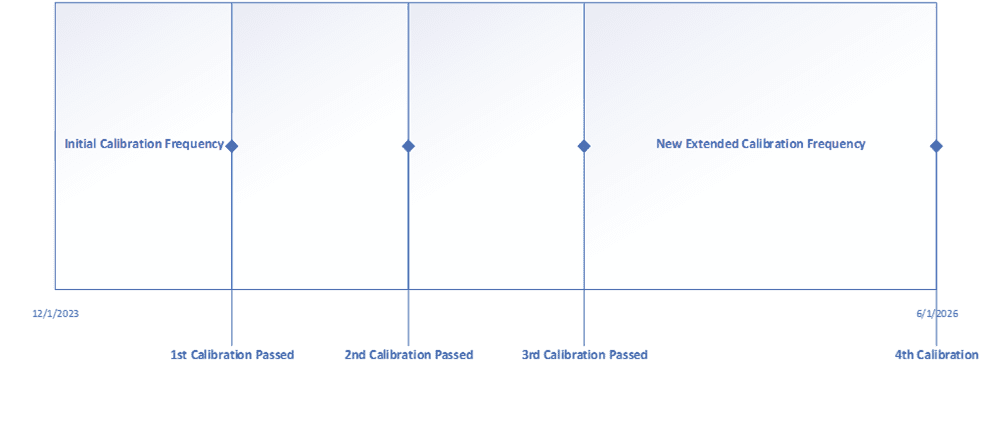
La ampliación de las frecuencias de calibración es donde más se notará el ahorro de costes, ya que menos eventos de calibración a lo largo del año significa que los recursos pueden realizar otras actividades. Lo importante es actualizar los procedimientos existentes que puedan dictar las frecuencias de calibración.
Si tu organización se beneficiaría de la aplicación de un enfoque de la calibración basado en el riesgo, a CAI le gustaría ayudarte. CAI tiene experiencia interfuncional en validación, calidad, rendimiento humano, gestión de proyectos y mantenimiento y calibración. Deja que nos convirtamos en tu socio de confianza en la gestión de activos GMP.